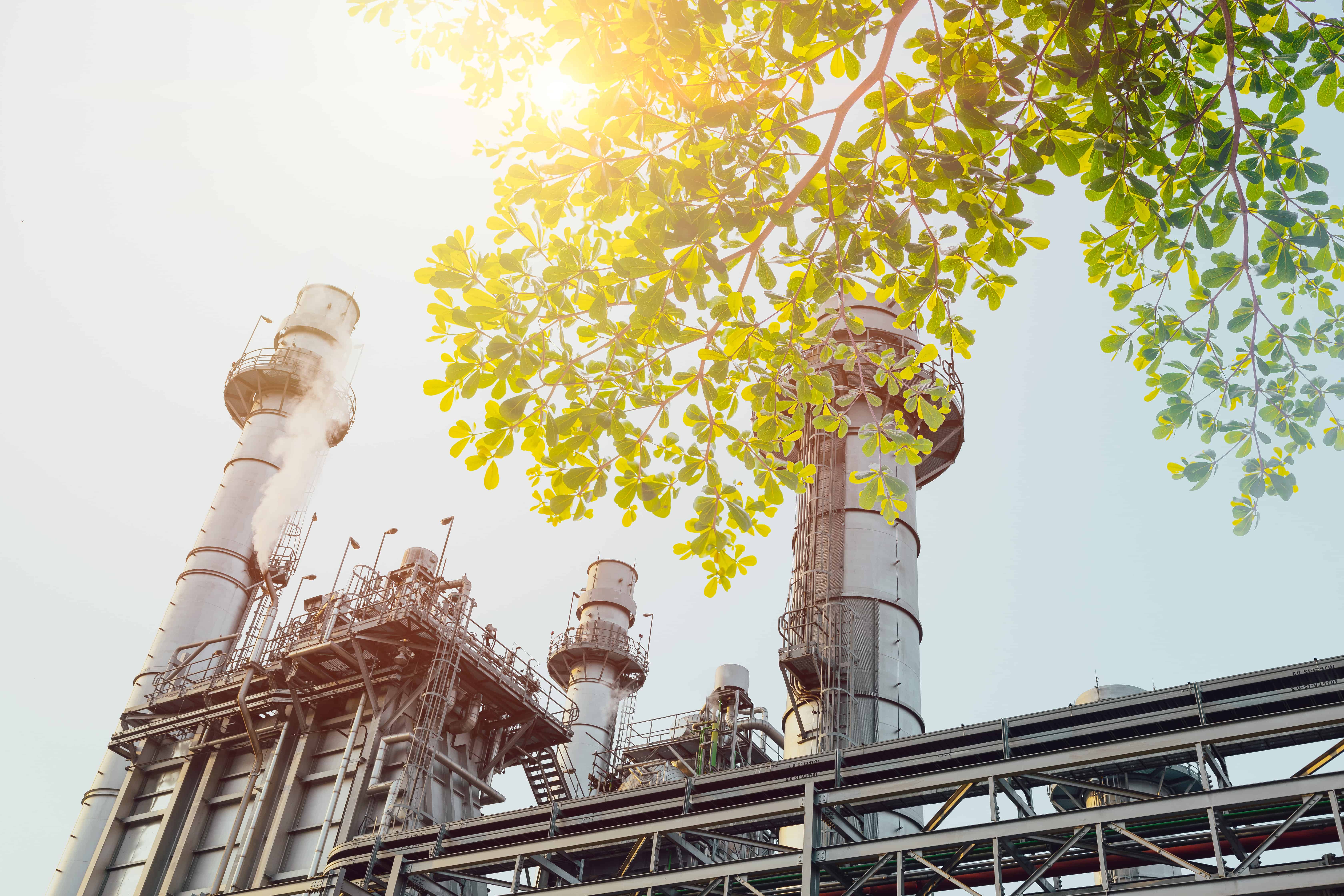
27 Jun Interview with Chris Faulkner, CTO at Agilyx
Could you introduce yourself?
I’m Chris Faulkner the CTO at Agilyx and have been in the sustainability sector throughout my career with a focus on stewardship.
As a technology leader could you comment on why Chemical recycling helps drive a cleaner more circular economy?
Today, the manufacture of plastics is primarily reliant on extracted oil and natural gas. Chemical recycling allows us to continue to use resources, that have already been extracted and have become ‘waste’, to create new, high-quality products and plastics. This reduces the need to acquire new fossil resources while also fostering more sustainable outcomes for post-use plastics – helping to eliminate plastic pollution and decrease landfill/incineration demand.
Many businesses today are seeking growth and faster market penetration through strategic partnerships. How has your partnership with Technip Energies and INEOS Styrolution helped drive successful outcomes?
Our modern supply and value chains are incredibly complex and when two large disparate industries (chemical and waste) intersect, partnerships and collaboration are essential. Our ongoing partnership with Technip Energies in the creation of TruStyrenyx™ has been a gamechanger for the recycling of polystyrene, bringing an integrated solution to waste polystyrene. The level of purity that we can achieve through our process, even when starting with distressed and contaminated waste polystyrene, opens value for waste materials that were previously thought to be too distressed to be recycled.
Early adopters of technology, such as INEOS Styrolution N.A., help demonstrate the market appetite and desire for recycled plastics and chemicals as well as the need for chemical recycling and more circular economies.
Your innovative process technology deals with polystyrene foam plastic. Does source variation or waste material availability create additional commercial challenges?
Our technology definitely provides a solution for waste polystyrene foam plastic as well as rigid waste polystyrene plastics. When developing solutions and technology for waste feedstock, indeed, feedstock variation and availability needs to be accounted for in an offering. Variation in feedstock is not limited to physical characteristics such as the form (rigid, foam, or film), shape, color, and size of the waste plastic but also the chemical nature of the waste feedstock such as non-polystyrene, non-polymer, hetero-atom species, halogenated contaminants to name a few. We developed TruStyrenyx™ to be robust and handle both physical and chemical variation in the waste feedstock while still maintaining high quality styrene monomer product. The more variant tolerant a technology the more addressable the waste feedstock availability becomes. This is where we view TruStyrenyx™ and Agilyx technology plays well.
Initially the chemical recycling industry, at large, focused on the conversion black box of taking waste plastic to something valuable. As technologies are becoming more available, the industry has now added focus to waste feedstock availability. Agilyx recognized the feedstock challenges early on in its formation. This is a large part of the reason Agilyx formed Cyclyx International, as a joint venture with ExxonMobil. Cyclyx is an ISCC+ certified waste sourcing and processing business which characterizes waste plastics according to their chemical composition as well as physical attributes, providing waste plastic feedstock solutions to mechanical and chemical recyclers alike.
The article talks about Polystyrene, but the picture shows Expanded Polystyrene, is the process limited to EPS, or is any type of Polystyrene able to be processed with this technology?
The technology being used in the project with INEOS Styrolution in Illinois is compatible with many types of polystyrene waste: EPS, XPS, HIPS, and GPPS to name a few.
Can you comment on if or how this technology could be leveraged to treat other plastic wastes? If so which ones?
Our patented depolymerization technology is suitable for multiple chemical recycling platforms: 1) plastic to monomers such as polystyrene and polymethyl methacrylate (PMMA), 2) mixed plastic to base chemicals such as olefins or aromatics, and 3) mixed plastic to low carbon fuels. One of the advantages to our technology is its robustness and applicability to several product pathways. This advantage also manifests in the technology’s ability to accommodate particularly distressed waste plastic, that would not be recycled otherwise due to contamination or source variation as mentioned previously. In addition to the polystyrene projects, we have announced projects for the chemical recycling of waste polymethyl methacrylate (PMMA – for example, used plexiglass) back to its monomer methyl methacrylate (MMA). Most recently we also announced development with BioBTX for recycling mixed waste plastic to BTX (benzene, toluene and xylene).
An exciting development for BSEF was your announcement that the technology can handle flame retarded. Could you tell us more, including how much of such foams are processed?
Indeed, the announcement of TruStyrenyx™ technology and its ability to accommodate brominated flame-retardant foams is exciting. Not only were our teams, Agilyx and Technip Energies, able to incorporate the foams as part of the feedstock for TruStyrenyx™, we demonstrated that the technology is able to accommodate a feed comprised of 100% brominated flame-retardant foam without compromising styrene monomer product quality.
Given your work and looking forward would you consider Bromine to be an issue for achieving a circular economy?
All chemistries should participate and aspire to achieve circular economy principles – bromine is no exception as it is critical to many chemistries employed today. In plastic chemical recycling, halogens, not just bromine, can pose a challenge that must be overcome as TruStyrenyx™ has achieved. With our technology and our partner’s purification process, bromine is not an issue for us in creating a circular economy for polystyrene.
While bromine and halogens may still cause issues for the recycling at large, with the right collaboration and partnerships, I believe innovative solutions could accommodate bromine as well. This has certainly been the case for TruStyrenyx™.
What is next? Will additional plant investments or greenfield projects be part of future plans as the marketplace develops an appetite for your reclaimed polymer streams?
Agilyx will continue to bring its existing technologies in waste polystyrene, mixed plastic, and PMMA to market, while simultaneously creating additional circular solutions.
The early stage of our development followed the classic build-own-operate approach that many others in this space are now following. With the development of the technology to include multiple conversion pathways, we shifted to an asset-light business model focused on monetizing the years of development in both conversion technology and feedstock insight through a combination of licensing, project development and provision of the critical core equipment.
In the current macroeconomic environment, capital allocation decisions can tend to take more time and therefore we are exploring other ways to progress facilities. This includes alternative funding sources to bring together a package that enables the customer to have an offtake agreement.
Is there anything else you would like to inform our LTB readers about?
We would like to thank BSEF for the opportunity to discuss our exciting TruStyrenyx™ technology and its associated projects. Additionally, we encourage the Bromine industry to participate in the developing circular economies as circularity is inherently more efficient than the make-take-waste model of the past. This is an exciting time in the chemical industry, and we look forward to the innovation and circular solutions to come.
No Comments